To help our portfolio companies navigate through the current “fog of uncertainty”, we have decided to write a series of articles in which we’ll delve into the impact of the Covid-19 sanitary crisis on our areas of expertise: energy, mobility and industry 4.0.
In these articles, we will analyze the impact over three different periods identified in our first article:
- Quarantine period — Fighting through the sanitary crisis (10–15 weeks in the UE)
- Safe-mode period — Learning to co-exist with Covid-19 (after quarantine)
- Period of recovery — Development and distribution of a vaccine at large scale (from 2021)
Introduction
In February 2020, the global manufacturing sector suffered its sharpest contraction since May 2009, as the spread of Covid-19 disrupted global supply chains and exerted a downward pressure on demand, production, and revenues. The organization of the manufacturing sector into global value chains — which has created dependencies largely beyond the control of individual businesses — has exacerbated the impact of the crisis, leaving most companies in the sector in a vulnerable financial state.
Against this backdrop of turbulence, what can manufacturers do in the short term to safely resume operations and get back on track? Will the Covid-19 crisis usher in the Golden Age of digitization in modern manufacturing? Which startups are best positioned to thrive in such an environment? In this article, we will share our insights of our discussions with different stakeholders on how they are responding to the crisis.
Phase 1: Quarantine period — Fighting for survival
For players across the board, Phase 1 consisted in protecting themselves from the pandemic and the risk of a — potentially massive — health related downside.
For corporates and SMEs, the priority was to safeguard their employees and to ensure business continuity. Most manufacturers were in ‘survival mode’, fighting to survive, focusing on lean operations, adopting digital tools for basic business processes, and cutting costs. As demand fell — unevenly across consumer, intermediate and investment goods — industry dynamics played a huge role in how businesses were affected. Manufacturing companies that were directly involved in the management of the crisis (medical supplies, basic necessities, etc.) fared better than verticalized players on the fringes of the ‘firefighting’ process (e.g. the automotive industry). While other players shifted parts of their business to support the war economy when the demand and supply of their existing products collapsed — in the US, Ford, in collaboration with GE Healthcare, 3M and UAW, manufactured respirators and personal protective equipment (PPE) to help fight the crisis in March and April.
For startups in the Industry 4.0 space, the impact of the virus was clearly felt on the sales cycles, with decision- making in SMEs and corporates being put on hold. Some startups therefore addressed other more dynamic verticals, such as the food distribution industry. “Some of our large food and drink customers are considering building their own additive manufacturing capabilities, to cope with the disruption in their supply chain for spare parts, and keep their manufacturing line running with parts printed on-site”– Omer Blaier, Co-founder & CEO, Castor.
For blue collar workers in manufacturing, it was an ‘interesting’ time. In some countries, such as the US, cost-cutting initiatives negatively impacted the workforce as the disruption of supply chains and social distancing measures put millions of employees out of work. In European countries, however, governments stepped in to pay wages for a limited period of time. This was done to avoid mass layoffs and to circumvent the bureaucratic complications that accompany the dismissal and hiring of workers. As operations came to a standstill, many firms became aware of the indispensability of blue-collar workers in the manufacturing industry. In the near future, this realization could mean a shift in the way manufacturing workforces are structured, with an emphasis on the upliftment of blue-collar workers. We could also see the middle management lose their bargaining power as of result of short-term cost reductions and the long-term increasing task automation — numerous recent studies show that operating without the middle management has increased the productivity of some manufacturers. This crisis will undeniably lead to organizational changes in the long run.
Phase 2: Charting the path to recovery
As countries begin to lift lockdowns restrictions, manufacturing businesses will be among the first to go back to work.
To prevent a second wave of infections, businesses will need to prioritize health over speed — an outbreak of infections would not only have a direct impact on the production capacity and the bottom line, but also on worker morale. Therefore businesses, especially manufacturers, are going to be obliged to find ways of resuming operations while respecting the hygiene and social distancing best practices. In this respect, businesses can draw inspiration from the world’s largest automobile plant, the Volkswagen plant in Wolfsburg, Germany. After closing the plant for more than 5 weeks, the company implemented 100 safety measures, determined in collaboration with the frontline workforce, to ensure a sustainable return to work. These measures include reducing the workforce (8,000 production line workers per shift instead of 20,000), social distancing measures, and strict disinfection guidelines.
However, a greater emphasis on health and safety measures will seriously reduce business productivity in the short term. This, in addition to low demand, will likely incentivize businesses to invest in digitization. Digital tools will help businesses to ensure business continuity and maintain a sufficient level of operations to serve the customers they retain. In light of social distancing best practices, several corporates are choosing to have their non frontline workers work from home — PSA, for example, announced a switch to remote work for all its white-collar workers after the deconfinement in France on the 11th May. In the US, the share of employees working remotely full-time in the manufacturing industry has jumped to 61% (up from 2pp before the crisis).
In this new work environment, the swift adoption of digital tools for communication, teamwork and managing business processes can greatly accelerate the return to work. Keeping business continuity in mind, the following categories of tools are likely to see accelerated adoption during this phase:
- Remote communication and teamwork tools: as frontline workers cannot work remotely, there is an urgent need to improve the effectiveness of internal communication (among blue-collar workers on the field and between blue-collar and white-collar workers). While tools and workarounds (such as SMS, telephone calls or WhatsApp) are not designed for operational excellence, we expect an increased adoption of dedicated tools — such as Beekeeper, Kraaft (for internal communications) and Yoho (to manage health concerns) — to ensure workforce productivity and seamless communication between remote teams.
- Support function tools: the digitization of support functions in the industry space — which is generally not the focus of innovation projects — could help businesses manage workforce, cybersecurity, and finance risks. A shift to remote work could imply greater reliance on the cloud, therefore VPNs and enhanced infrastructure security. As businesses implement health insurance and government-mandated policies internally, functions such as HR and compliance could also experience increasing digitization in the near future. Financial management will also be crucial as companies explore new business models and take stock of the fiscal conditions of their suppliers and customers.
- Tools supporting core internal business processes and analytics: when factories resume their productions, the monitoring of production KPIs will be greatly facilitated. However, businesses operating in globally distributed value chains will be more affected, as employees may not be physically present to monitor quality and performance metrics. “Monitoring and maintaining the ongoing production process has become impossible for many companies. Digitizing global monitoring over the entire manufacturing cycle has become a critical need to regain control and end-to-end transparency.” — Eyal Kaufman, CEO, QualityLine.
- Contingency planning and scenario modelling tools: in the short term, shifts in the global social and geopolitical climate, disrupted supply chains and changing customer preferences will require manufacturers to be agile and have visibility across the entire value chain. Companies will have to anticipate disruptions both upstream (plan for more flexible sourcing, replace hard-to-get parts, produce hard-to-get part in-house, etc.) and downstream (customize their value offering to meet more local needs). They also need to adapt to potential changes in the customer journey, encompassing shifting demands and adapting to new customer engagement models. To better understand our perspective on supply chain disruptions, you can read Raphaëlle’s article.
Prior to the crisis, corporates’ priorities regarding digitization were operational efficiency, capturing competitors’ market share and impacting share price and dividends. During Phase 2, however, the focus is now on ensuring business continuity, capturing emerging market shares and offsetting debt from their balance sheets. As a result, the digitization projects that focus mainly on improvement (of processes/ products, etc.) could be relegated to the background in the medium term — the severe financial impact of the crisis is making companies reluctant to embark on non-core projects, especially where the ROI is not clear.
Phase 3: The Golden Age of digitization in manufacturing?
Once we enter the ‘new normal’, businesses will need to focus on protecting themselves against future uncertainties (brought on by bigger threats such as the impact of climate change). Our hypothesis is that, with continued strategic investment in digitization — and subsequently, automation — they could make themselves ‘antifragile’.
Traditionally, executives in the manufacturing industry have inched cautiously towards digitization, although they recognize the competitive edge that it brings. This is due to the complications of project conception, change management and deployment at scale. During the crisis, however, some companies have demonstrated impressive agility in adopting new ways of working to ensure business continuity. Microsoft, for example, reported at the end of April that they had seen two years of digital transformation unfold in two months.
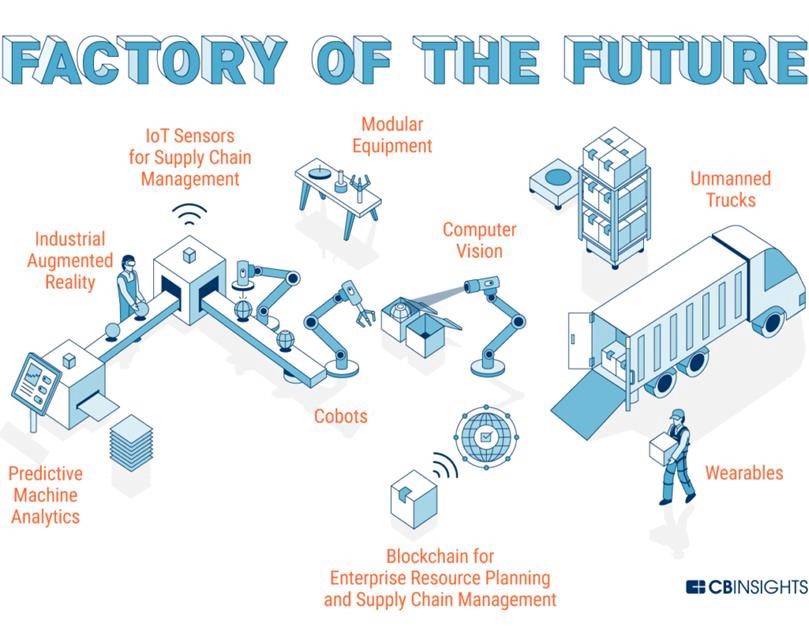
When it comes to digitization in the factory, change management (not technology) is the bottleneck.
The need for flexibility and resilience (in addition to focusing on productivity and quality) could be the driving force behind digitization. The case for digitization in the manufacturing industry is reinforced by the way technological advancements (such as data access, computing power, machine connectivity, business intelligence and HMI technologies) can impact business metrics (productivity, downtime, quality, flexibility, time to market). In an uncertain post-pandemic world, businesses will need to be agile to thrive, and end-to-end visibility across the value chain will be at the heart of those efforts. Specifically, businesses will need to have better visibility into the availability of raw materials, inventory, WIP, people and assets. This visibility will then need to be translated into timely decision making: “As a direct result of the crisis, companies are facing demand uncertainty and have constrained supply chains. They are looking for ways to be resilient and flexible in how they manage operations — the goal is to increase transparency and collaboration with both customers and suppliers while reducing operating costs. Investing in digitization to improve the productivity and proactive decision-making capacity of the white-collar workforce (supply chain managers, production controllers, quality inspectors…) with advanced analytics will result in massive efficiency gains.” — Tarik Benabdallah, CEO & Founder, Pelico.
On the factory floor, automation will still consist of optimizing the interaction between man and machine, and not of deploying robots. Until now, automation in factories has been less about replacing machines and equipment than it has been about harnessing captured data and making machines and human workers smarter and more efficient. Today, in a typical factory, robots perform ca. 10% of tasks, a number that could reach a maximum of ca. 25% in 2025. That is not expected to change in the short term — human agility and judgement are indispensable on the factory floor, especially when it comes to non-standardized processes in unpredictable environments. Robots are suitable for high volume situations requiring accuracy and speed, but fail when time to market and customization are the KPIs of interest to the factory. In fact, in the mid-2010s, Toyota replaced robots with human workers because the robots did not meet their accuracy and process improvement expectations. In addition, there is a skill gap when it comes to designing, programming, running, deploying, and maintaining robots which indicates that we are unlikely to see large-scale robot-led automation in manufacturing anytime soon. Manufacturers should focus on deploying robots where it is cost-effective and frees up capacity for human workers. This does not mean that a wave of robot automation is totally out of the question in the mid to long term. Players such as ABB (in collaboration with AI startup Covariant) are working on tackling tasks that typically require human intervention (early adoption is in logistics, but they foresee adoption spilling over into manufacturing too soon).
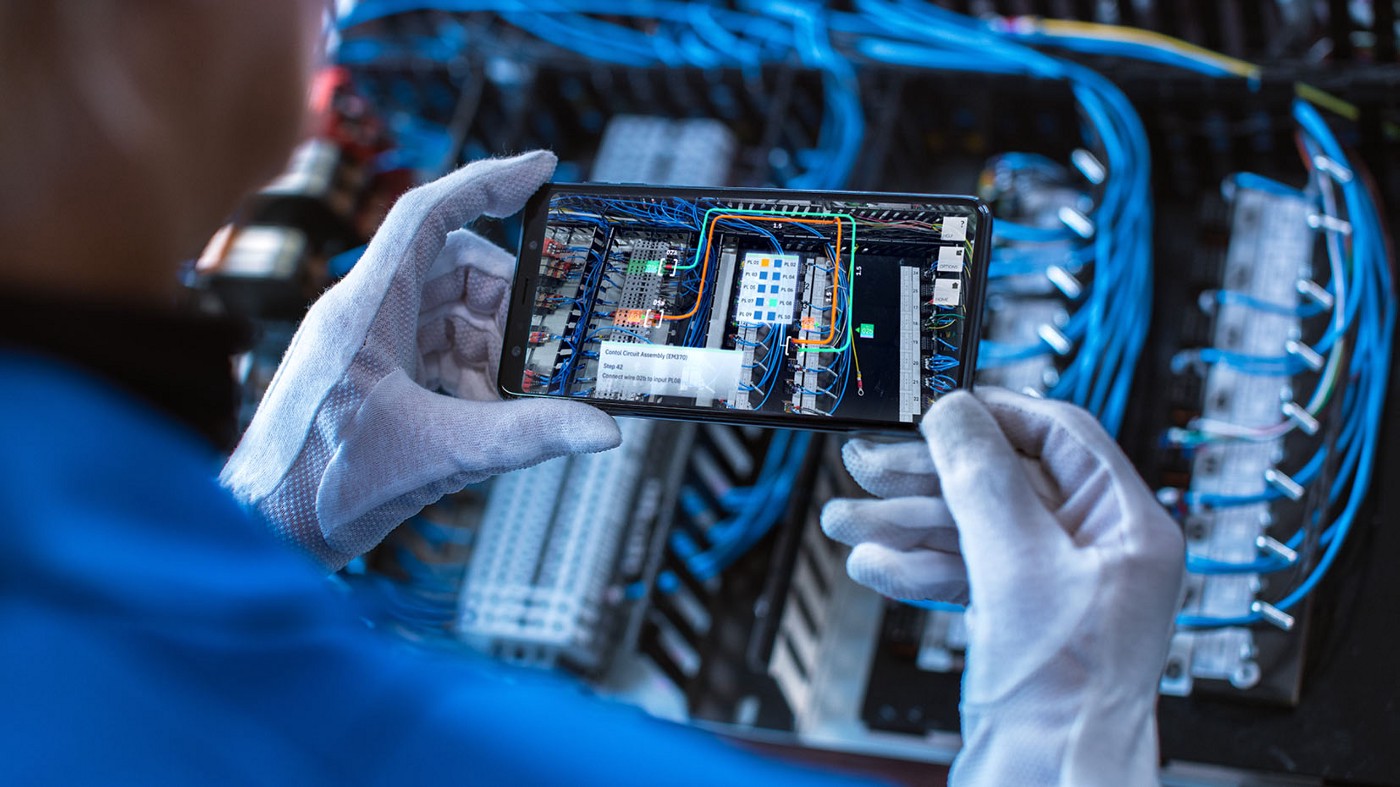
The future of work in manufacturing centers around the augmented frontline worker.
Companies will probably need to invest in training workers for the ‘reimagined organization’. The crisis will highlight systemic HR inefficiencies and the accelerated adoption of digital tools will redefine many jobs. Historically, new technology and automation have played an instrumental role in the evolution of jobs and work. Industry leaders recognize the latter, and the reskilling and upskilling of the workforce has been a hot topic for businesses and governments in the face of Industry 4.0 for some time now. As companies scramble to digitize and automate to ensure business resumption, they also face the challenge of adapting their processes and reskilling/upskilling their workforce to prepare for the post-pandemic world. According to Jorim Rademaker, CEO of Manual.to, “In an Industry 4.0 setting, the frontline worker needs to become increasingly interoperable. Rising automation, IoT and big data analytics, put strain on the human operator, who is at risk of becoming a bottleneck. Facing increasing demands and complexity, the human operator needs easy, effective and engaging digital tools, encompassing training, performance support, and information tools. An aging workforce, and an influx of generation Z workers introduce additional challenges. It is in this rapidly changing world that operator-centric digital knowledge sharing tools like ours — Manual.to — offer groundbreaking and sustainable advantages.”.
Conclusion
The manufacturing sector is one of the hardest hit by the crisis, but it is also one of the best placed to leverage digital transformation to reinvent itself and emerge stronger in the post pandemic world. What the near future holds for manufacturing businesses will depend on the robustness of government intervention, the duration of the crisis, and their agility to bounce back.
The central role played by frontline workers has been highlighted during this crisis, and many corporates may now realize the urgent need to augment their workers in order to be better equipped for the road ahead. While increased digitization and automation will destroy some jobs (impact on middle management and gatekeepers such as IT), it will also reform others (jobs on the factory floor).
Advice to the manufacturing startups: if you can, offer services free of charge to help fight against Covid-19. It is harder to get budgets for software rather than hardware for safety but it is good to open positions. The startups that adapt their value proposition (according to the evolving needs of their customers) while having a quick ROI will come out of the crisis with a stronger foothold in the market. Startups whose value propositions are flexible enough to explore new market segments should also explore this option.