From 2014 to 2019, VC investment in European industrial tech startups increased from €100m to €1.1b. However, despite this impressive growth, industrial tech accounted for only 3% of all European VC funding in 2019. Interestingly, there is a sharp contrast between VC funding in industrial tech, and the actual contribution of the industrial sector to the economy. Indeed, in 2020, the manufacturing sector accounted for about 22% of the EU’s GDP. In addition, the European manufacturing sector, which is amongst the least digitized, has been suffering from a decline in productivity growth over the past 15 years and is facing increased competition from foreign players. As such, we firmly believe that the European manufacturing sector will need startup-driven innovation to boost its productivity and thereby increase its competitiveness.
This begs the following question: how can manufacturing companies become more productive?
There are many ways to answer this question, but today we will focus on how the industrial tech stack can lead to productivity improvements in manufacturing. First, we need to understand what the industrial tech stack actually is. The industrial tech stack is a complex structure composed of 4 layers, each containing software and hardware components:
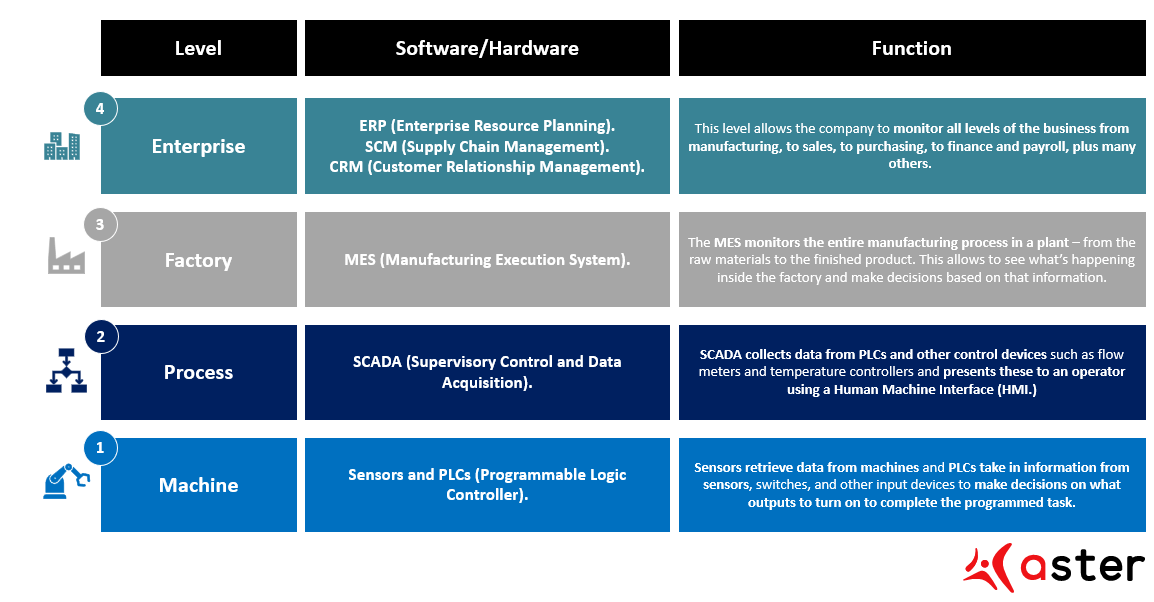
Source: Aster
Unfortunately, in most factories, the tech stack is full of inefficiencies:
- Old unconnected machines: it is not uncommon to find aging, sensorless equipment on the factory floor, as replacement cycles for heavy assets often last decades.
- Unconnected stack layers: PLCs are not necessarily connected to SCADA systems, the SCADA system of different processes are not necessarily connected to each other, and the MES is not always fully connected to all processes in the factory.
- Lack of data harmonization and interoperability: factory data can come from many different sources (sensors, SCADA, MES, Excel sheets, PLCs, …) and in many different forms (structured, semi-structured or unstructured). In addition, machines and software used in factories can be quite old, often come from different suppliers, and often have different communication protocols.
- Lack of IT/OT collaboration: the firm (IT) and factory (OT) levels are often not fully integrated, resulting in a poor understanding of factory processes at the firm level. The factory is basically seen as a black box by the firm level, and this is called the “IT/OT convergence” problem.
Clearly, we can see that the main problem with traditional tech stacks is that industrial data is hard to collect and difficult to integrate. Without access to industrial data, implementing use cases that lead to productivity improvements – such as process optimization, predictive maintenance or automated quality control – is quite challenging.
We believe that startups can help manufacturing companies improve their industrial tech stack in 3 different ways:
- Data collection: provide hardware/software to connect old legacy machines to IT/OT networks and provide middleware or connectivity to facilitate data collection from sensors and machines.
- Data harmonization: provide software to integrate, harmonize and generate insights from industrial data across the factory floor or even across different factories.
- Decentralization: bridge the gap between the firm- and machine-level through edge-computing, allowing machines to interact with each other and take more autonomous decisions. The idea is to connect machines to each other, to operators and to the firm-level in order to have flexible production lines that take into account not only factory (OT) data to take decisions, but also firm (IT) data. For example, this structure could enable machines to change their parameters automatically to produce different products based on demand forecasts made at the firm-level.
Our view is that the future industrial tech stack will be decentralized, and we look forward to seeing more companies contributing to this trend. However, in the short- to medium-term, we believe that there is value in helping manufacturing companies through data harmonization. As such, we believe that startups that will stand out in the space will be those that:
- Harmonize and contextualize structured/semi-structured/unstructured data from a large number of sources (MES, SCADA, PLC, sensors, Excel sheets, …) and are able to easily integrate into the existing stack of customers.
- Provide a clear and measurable ROI to customers.
- Enable the interconnection of devices in manufacturing operations with a low-code/no-code approach.
- Focus on making production lines flexible, more autonomous and directly connected to the IT level.
- Provide edge computing with a low latency, low costs, AI and ML capabilities, real-time analytics and focus on working towards IT/OT convergence.
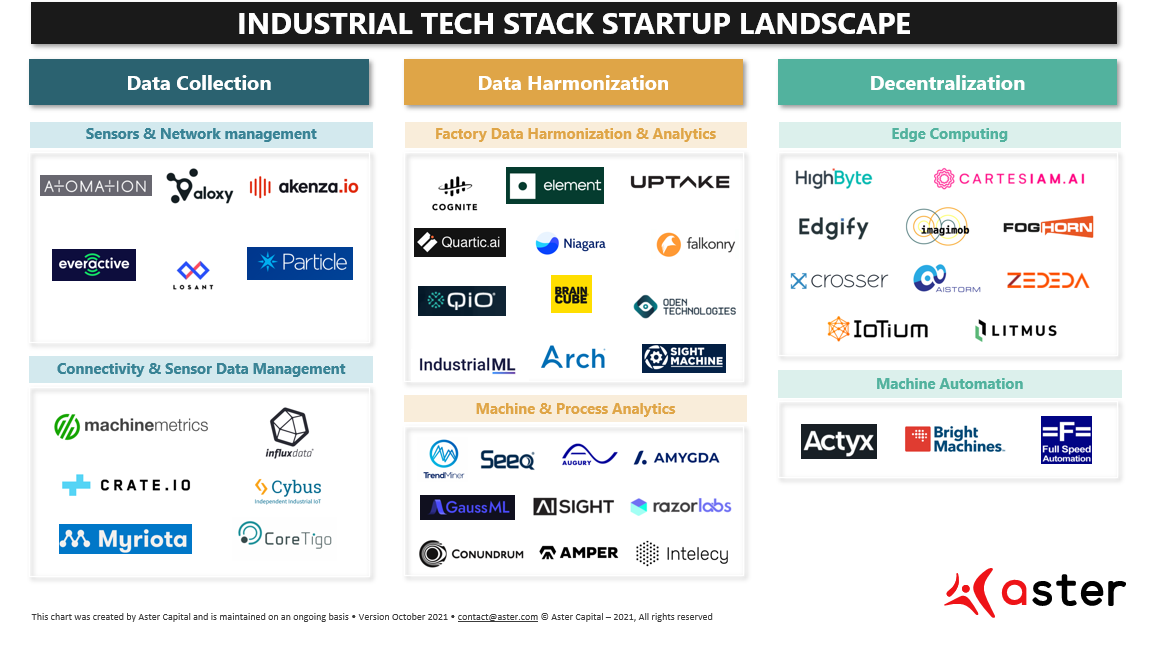
Source: Aster